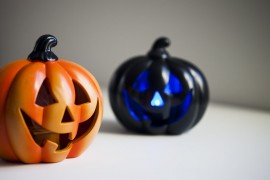
Three creasing machine horror stories about sheet feeding problems you need to avoid-
Our latest blog takes a scary look into creasing machine feeders. Read on, if you dare…
It goes without saying that the main purpose of a digital creasing machine is to apply the type of high quality creasing application that leads to the elimination of toner cracking, right?. Well, I feel there is an equally critical process involved in the operation that comes before the act of creasing, yes you’ve guessed it, feeding. OK, feeding digital stocks consistently and accurately might be seen as something that is expected, or even taken for granted, but I can assure you that there are horror stories that circulate in our industry that warrant some further exploration, take for instance these three cases.
- Miss-registering horror story
There was the story about the printer who was shocked to find that his 16,000 furniture leaflets, printed on 90gsm gloss were cracking as he processed them through his bench top folding machine. He’d never had to crease paper before and was cursing the fact that an abundance of toner had caused the problem and resulted in production grinding to a halt. It looked as though an hour’s run through the folder would now be preceded by a few hours of throughput using his automatic matrix creaser.
After 20 minutes of fighting the air valves in the feeding section of his creaser to reduce the flow of air dispersion into his paper sheets (which were flying all over the place) and 5 minutes of trying to reduce suction from his vacuum pump, he was ready to go. The first sheet appeared to register correctly and his hand folding proved, as usual, that all was good. Unfortunately, the next five sheets didn’t bring about the same outcome, every leaflet folded differently. It turned out that the paper leaflets kept buckling and miss-registering as they stopped in position before the creasing rule struck and the wide crease made the fold vary even more. The poor printer didn’t realise it at the time but his creaser wasn’t designed to feed or crease paper. The manufacturers hadn’t thought that they needed to test paper substrates below 100gsm. They had only focussed on processing 130gsm stock and above, it used to be 170gsm and above but digital print brought about more changes and the minimum stock weight changed. No problems at all, simply because 130gsm has rigidity and stiffness that allowed this type of sheet to feed and hold strong through the creasing process. Unfortunately, those leaflets were printed on 90gsm substrate and were not rigid enough to prevent them from buckling, yielding or slipping in that crucial stop position before the crease was implemented, resulting in erratic fold variation.
- Heavy sheet load horror story
The MD of an offset printing company was trying to get into the digital market by purchasing a Xerox printer and an automated creaser. He was used to faster production but understands the nature of digital print, which equates to shorter print runs and slower output speed. Unfortunately, he hit an early problem connected with processing 25,000 A3 menus, litho printed on 350gsm board and laminated both sides, no matter how hard his finishing operator tried; he struggled to feed the sheets through the creaser with any degree of consistency. Putting 20 sheets in the feeder wasn’t a problem as the air filtered through perfectly, but the feeder kept running out whilst he collated the finished product and placed them in a box. Piling in 100 sheets would have been ideal, leaving enough time to pack the menus and get back to feeding – sadly, it was like trying to feed a block of ice, the load was so heavy, hardly any air was getting through to separate the bottom sheets, no matter what he did to the vacuum pump – the operator spent twice as long processing the menus and as this was a monthly repeat job he wasn’t looking forward to the next battle!
- Friction feed horror story
A print finishing manager bought a reconditioned friction feed/creaser, because he wanted to save money and overcome some of the issues mentioned in horror stories 1 & 2. After all, friction feeding can deal with separating and processing light and heavy stocks much more efficiently than suction/vacuum feed methods, but there is a massive downside, as our print finishing friend was about to find out. He ran off 10,000 digitally printed leaflets without noticing that the cheap rubber friction wheel had scuffed every one of them. He had heard some bad things about friction feed marking, but ignored them. He spent the rest of the day worrying about coming clean and telling the customer about those scuff marks that appeared in a prominent position, he will certainly think twice about processing anything that is digitally printed in the future.
A solution that ends three horror stories about feeding
In my line of business I often hear comments like this, “friction feeding will never be accepted as a solution to feeding digital stocks because it scuffs the toner.” Another statement may sound like this, “vacuum methods are the only true and reliable methods to feed digital stocks.”
Well, if you have carefully read the three horror stories above you will in fact see some common problems that get repeated over and over again, all pointing to the fact that there is no true and reliable feeding method that will successfully process every type of stock a digital printer may be faced with
When we developed our own automatic creasing machine we took time to study the three cases highlighted above and worked hard for three long years, to find out how we could overcome each one and develop a feeder that could;
- Easily feed and crease paper with precise crease register
- Easily feed and crease heavy laminated board stocks and retain a sufficient feed stack
- Guarantee no scuffing or marking digitally fed sheets
(In other words we wanted to create a feeding mechanism that could feed everything, with little or no effort involved in changing from one stock to another)
Our research, of course, confirmed what we as former print finishers knew already that paper obviously needs different air flow and suction control than board and we knew that some principles used in friction feeders, were also effective. In short we jumbled up the best of vacuum and friction and came up with our “Gravity Flow Feeder.”
Our Gravity Flow Feeder is connected to two of our CreaseStream Mini machines, and we are pleased that it allows users to do the following:
- Successfully feed and crease lighter paper without it buckling or slipping and with precise crease register, unlike what can be witnessed using vacuum methods
- Achieve continuity of feeding heavy laminated stocks and retain higher stack load than vacuum methods
- Feed more efficiently than using friction methods but without any trace of scuffing or marking
- Change from feeding one stock type to another within a few short seconds, without any drawn out resetting
Our Gravity Flow Feeder is unique in that it doesn’t require a vacuum pump or suction yet it outperforms many of the most popular air feed systems in the creasing market, without scuffing or marking the stock. The video below will show you our Gravity Flow Feeder at its very best, working on our CreaseStream plus model. The video underlines more technical information:
To receive our latest CreaseStream Mini brochure or to receive a price quote, email [email protected] or call +44 (0) 1455 5544 91